How Computer Aided Engineering Can Benefit Cable Manufacturing Industry
Filed under: Uncategorized
Comments: None
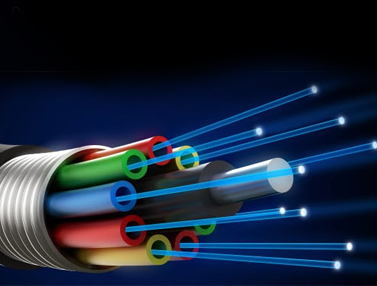
Industries that manufacture high-voltage cables are required to consider important design parameters when designing power transmission systems. One key aspect is the ability to deliver specified quantity of current without exceeding permissible temperatures. This requires designers to develop detailed thermal model considering all the variables such as cable structure, electric losses, installation geometry, environment where the cables will be installed and its proximity to other infrastructures, ambient temperature and effects of other external loads such as solar radiation.
Prior to the usage of CFD simulations, cable industry typically relied on empirical formulas and calculations as per international standards. While these mathematical equations work pretty well for systems installed underground, it becomes complex and cumbersome to develop a thermal model of new systems usually employed in the vicinity of existing infrastructures such as other cables and crossing regions often referred to as unfavorable thermal environment.
However, using multi physics simulation through computational fluid dynamics, extensive transient analyses can be conducted to study the effects of daily variations in solar irradiation and ambient temperature conditions. Current load changes can be directly applied against constant operating conditions to figure out actual scenario.
With multi physics, a parametric model can be built to optimize the geometry and cable laying arrangements based on the physics. This indirectly helps in improving the manufacturing processes as through simulation it is possible to decide the positioning of components such as power conductors and deliver hoses in cables.
Since computer simulations offer a clear perspective on what
Be the first to write a comment.
Your feedback